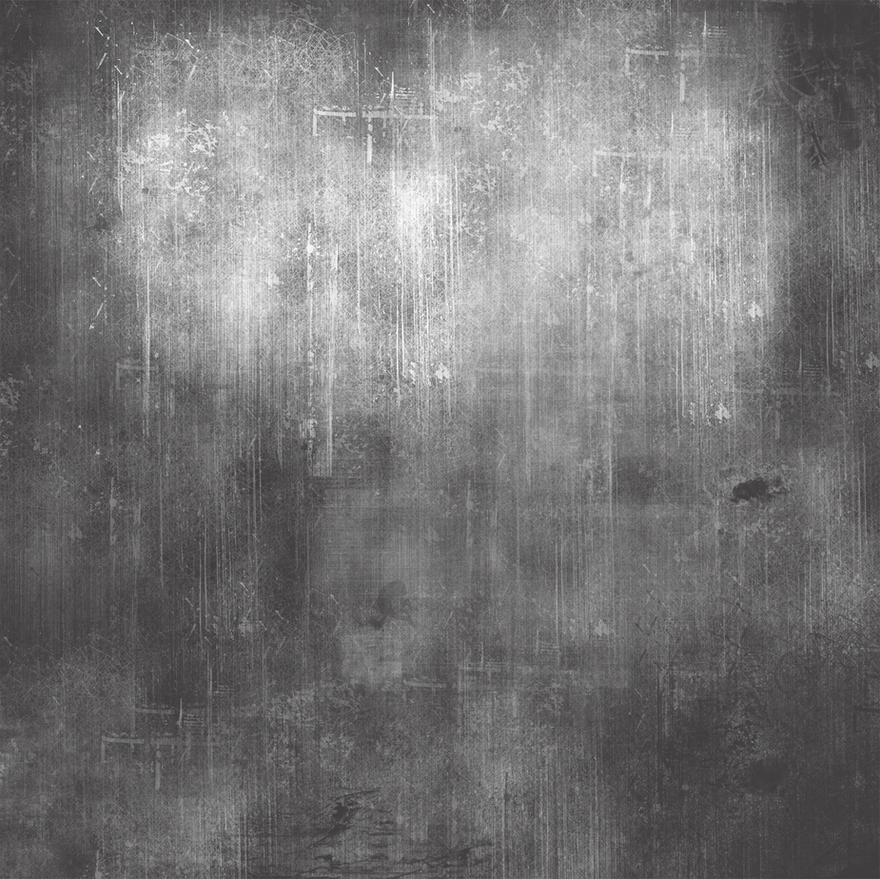
BIOMASS DRUM DRYERS
Tel.: + 420 734 620 779
Fax: + 420 518 322 329
E-mail: votona@votona.cz www.votona.cz
THE COMPANY GARD INVEST a.s. DEALS IN THE DISTRIBUTION AND SERVICE OF MACHINES IN THE EU; RUSSIAN FEDERATION AND BELARUS
The drum dryers are designed for small wood waste and biomass drying.
Wood residue: sawdust, cut wood, wood chips (pre-crushed up to 8 mm).
Input moisture before drying: 55-60%. Initial moisture after drying: 10%.
At present time, our standard dryers are available in the following performance classes:
up to 600kg/h, up to 800kg/h, up to 1000kg/h of finished material.
Our technology is exclusively manufactured to customer requirements
and on customer request! Build-to-order: from 1000kg/h.
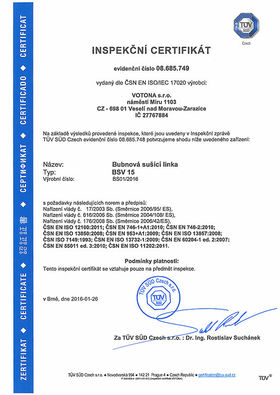



GARD INVEST
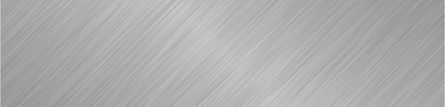

MACHINE COMPOSITION:
-
Material input section
-
Boiler 500 kW
-
Bunker with mechanical fuel supply
-
Coupling
-
Temperature sensor
-
Drum dryer
-
Conveyor-fan
-
Cyclone separator
-
Moisture sensor
-
Screwconveyor
-
Dry-chip-silo
-
Rotation speed control
-
Control panel unit
DIAGRAM AND WORKING PRINCIPLE OF THE DRYER
TECHNICAL SPECIFICATIONS:
Machine model: VOTONA-400/600
Output: 0,6 t/h
Raw Material: chips, wood chips
(pre-crushedup to 8 mm).
Maximumraw material
moisture content: 60%
Width for the Machine: 12х6 m
Height for the Machine: 4,5 m
Electrical power consumption of the
conveyor-fan: 30 kW
Electrical power consumption of the
screw conveyor (3 pcs.): 1,0 kW
Electrical power consumption of the
drum dryer: 1,5 kW
Numbers of operators per shift: 1 person
Attention! The mobile version of the site does not display all the information.
Principle – The drying principle is based on the principle of indirect drying by means
of heat exchangers.
This prevents the worsening of product quality by avoiding the contamination of the
dry material.
The material to be dried is sucked in with a conveyor-fan through a heat exchanger integrated in the boiler.
The moisture reduction takes place in the drum dryer. The geometries of the drum dryer are dimensioned in such a way that a uniform, homogenous drying material is produced.
During this process, contact between the hot gases and the biomass is excluded.
The technical implementation of our machines is carried out according to the applicable technical rules and by taking the applicable fire regulations in account.The “hot air” provided through the heat exchanger flows through the drying material held in suspension by the drum rotation and dries it.
The drying result is controlled in a targeted manner by regulating the supply of dry goods.
The speed of the material feed is controlled in the case of constant hot air flow so that a homogeneous finished material with a residual moisture content of approx. 8-10% +/- 1%
is produced at the dryer output.
The hot air is sucked through the dryer via a conveyor-fan.
At the dryer output, the drying material is taken over by the conveyor-fan and separated from the transport air by a cyclone separator.From the cyclone separator, the dry material
is then transported mechanically into the pre-press-bunker from where it is also continuously fed via mechanical conveying to the pressing.
Fuel – The following fuels can be used for the boiler:
Wood waste, cut wood, sawdust, wood chips,
Boiler – The boiler can be operated with manual or automated fuel supply via dosing devices.
All boilers are equipped with a measuring device for volumetric detection of fuel and automatic fuel supply.The interplay between the automatic and controlled fuel supply on the one hand and the controlled supply of drying material on the other hand guarantee
a uniform and homogenous drying result.
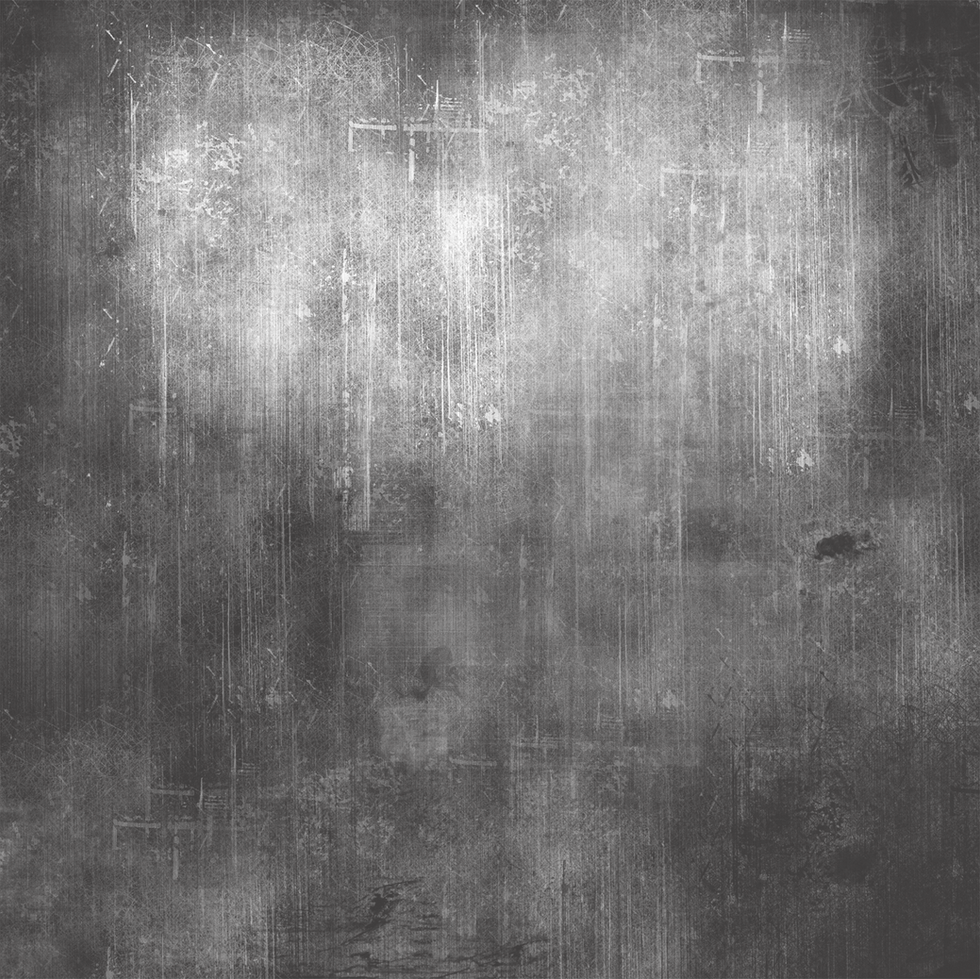
DESCRIPTION OF THE BASE ELEMENTS OF THE MACHINE
ADDITIONAL MACHINES, NOT INCLUDED IN THE PRICE
Execution options:
- Individual plant concepts according to customer requierements.
- Boiler without heat exchanger (drying process directly with hot flue gases).
- Flue gas ducts, branching, conjunctions, chimney.
Note: These are to be adapted to the position and the customer-specific locations and execution regulations.
- Mixing chamber for the separation of combustion and exhaust gases (only for boilers without heat exchanger).
- Discharge lines, fittings, etc, for the cyclone separator.
Note: These are to be adapted to the position and the customer-specific locations and execution regulations.
- Secondary separator for separation of ash and dust.
- Conveying means for material transport, e.g. floor conveyor, screw conveyors,
scraper-chain conveyors; conveyor belts etc.
- Dry-chip-silo for storage of the dried chip material.
- Moisture measuring device for monitoring and controlling of the dry goods with connection and integration into the dryer control.
Note: If the biomass is applied below the set parameters, overdried, the speed of the feed
device for wet material is automatically increased, thus increasing the material supply in the same way with constant heat energy supply.
This materially affects the material moisture at the dryer output and is adapted to the pre-set values.
In the case of a low initial moisture content (over drying), the feed conveyor is throttled and the material supply is reduced again analogously.
This ensures a constant drying result with very low moisture fluctuations!

DRUM DRYERS FOR BIOMASS. Production in Russia